San Francisco International Airport
Architect: |
HKSWOODS BAGOTED2KYA |
Location: |
San Francisco, CA |
Product: |
Custom Column Covers |
Application: |
Interior multi-faceted non-perforated column cover skins paired with a custom gradient perforation that also functioned as a HVAC diffusor. |
About the Project
The manufacturer provided 119 uniquely shaped, highly custom column covers for Phase 1 of this $2.4 billion aviation project. Each of the columns were made of multiple materials including 16ga galvanized steel with factory applied powder coat in both matte and satin gloss finishes. The lower bases were constructed with 16ga 304 stainless steel.
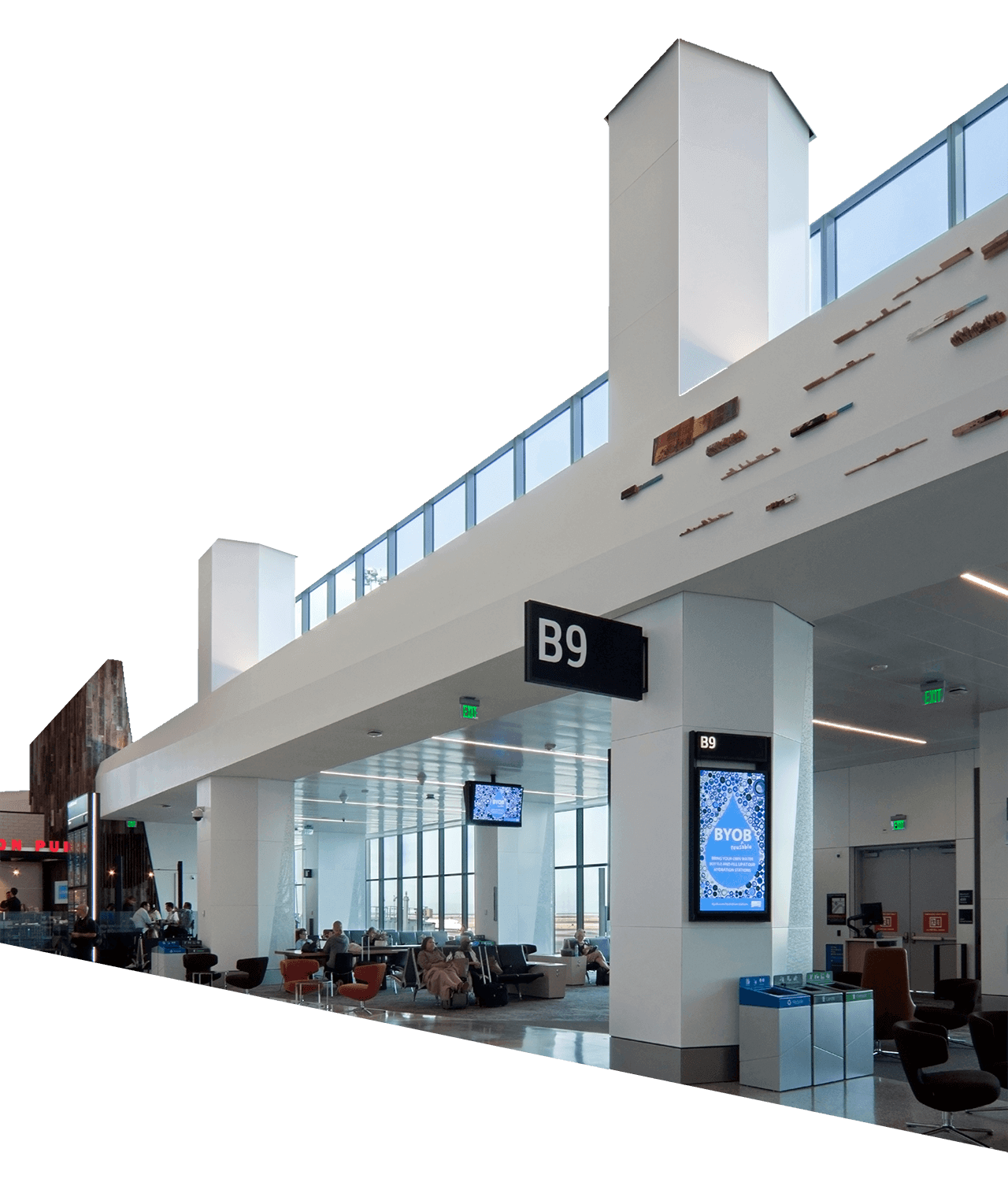
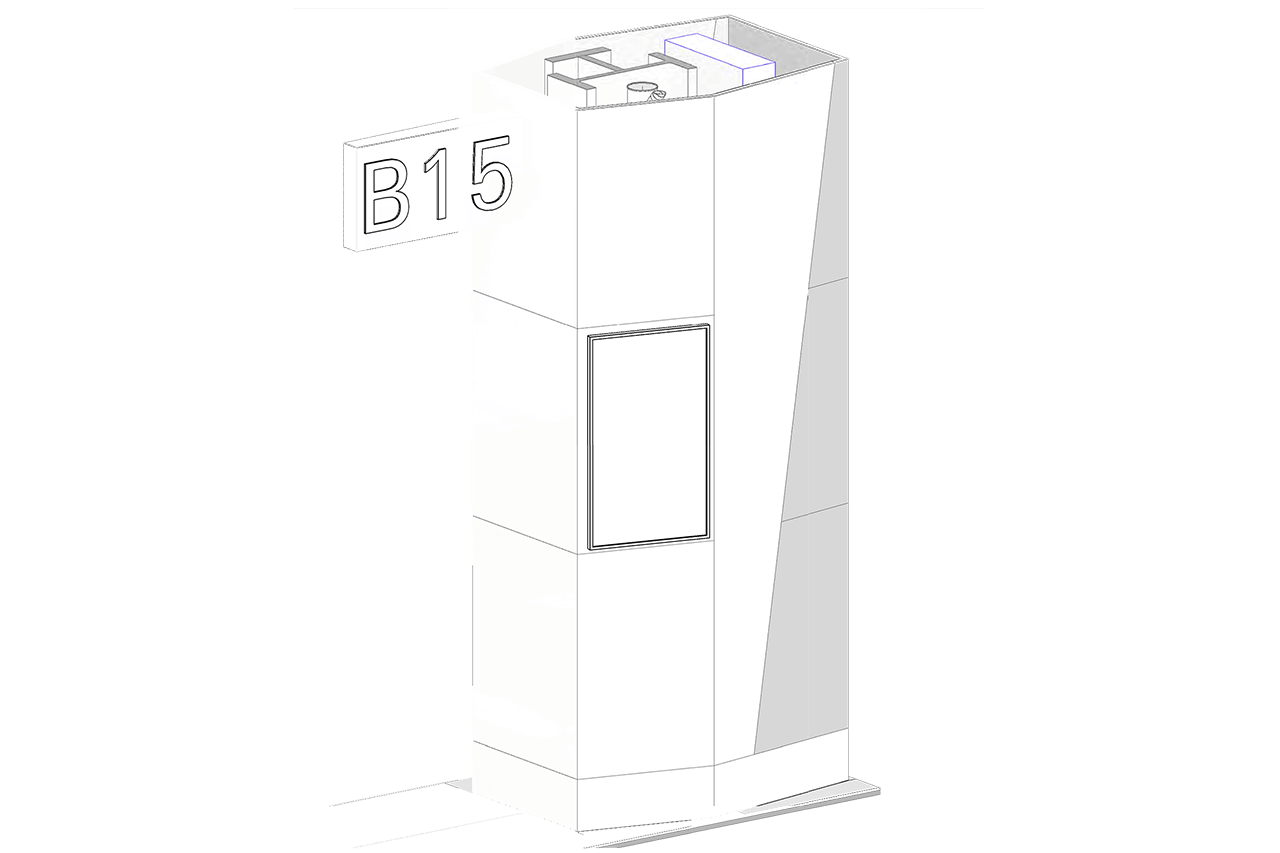
Concept
The column cover design served as both form and function. The finished product provided aesthetics to the space while serving as a conduit for M.E.P’s as well as a functional diffusor for the HVAC system. The percentage open area of the perforation was required to meet HVAC design criteria.
Other elements were incorporated into the design including airport surveillance monitors, thermostats, courtesy phones, fire extinguisher cabinets, electrical outlets, and gate and restroom signage. Informational laminates were also applied to selected non-perforated spaces on the columns located at various eateries.
Development
Gordon’s engineering team meticulously developed the attachments and connections for the unique column cover shapes. 3D models were generated to ensure the components came together to form a cohesive and functional column cover.
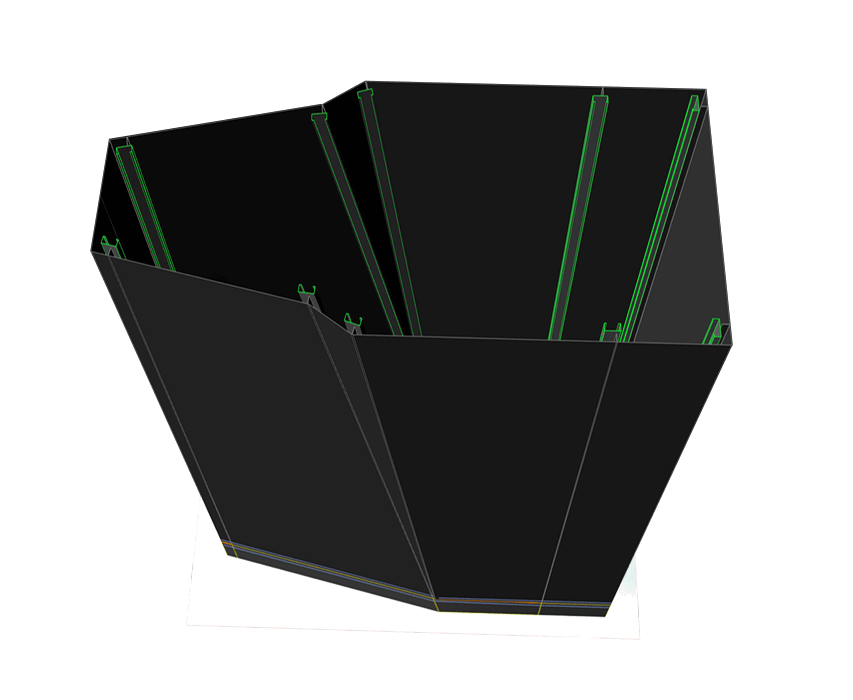
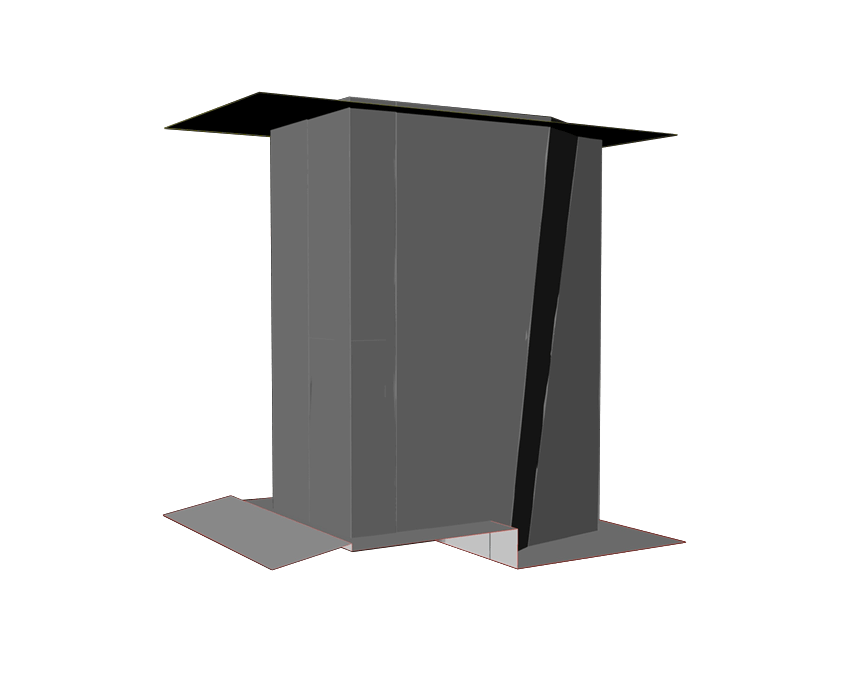
Innovation
The perforations were exceptionally custom in nature, featuring a gradient pattern that transitioned from a higher percentage of open area on the lower skins and a gradual transition in the form of a reduction in open area progressing to the top of the column.
The gradient perforation pattern went through several iterations during the design process in an effort to achieve a true “randomized” pattern void of a pareidolia effect or mirroring in the perforation.
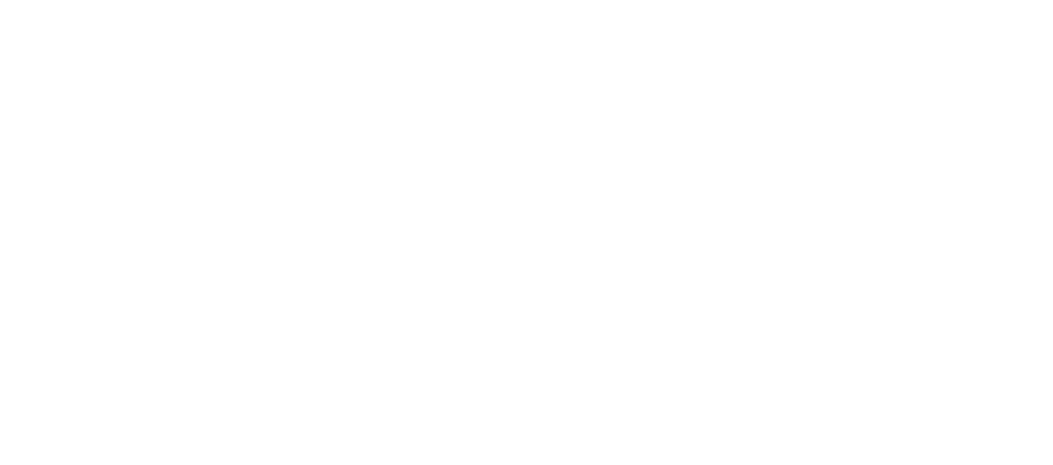
Craft
In 6-weeks total, the manufacturing production team fabricated, formed, assembled, powder coat finished, and packed 900 panels and assembly components. Essentially, the required 60-working days to manufacture and ship to the job site was compressed into a 30-day “manufacturing miracle”.
The entire design team, including the installing contractors, visited the manufacturer to review full-scale mock-ups of the columns.
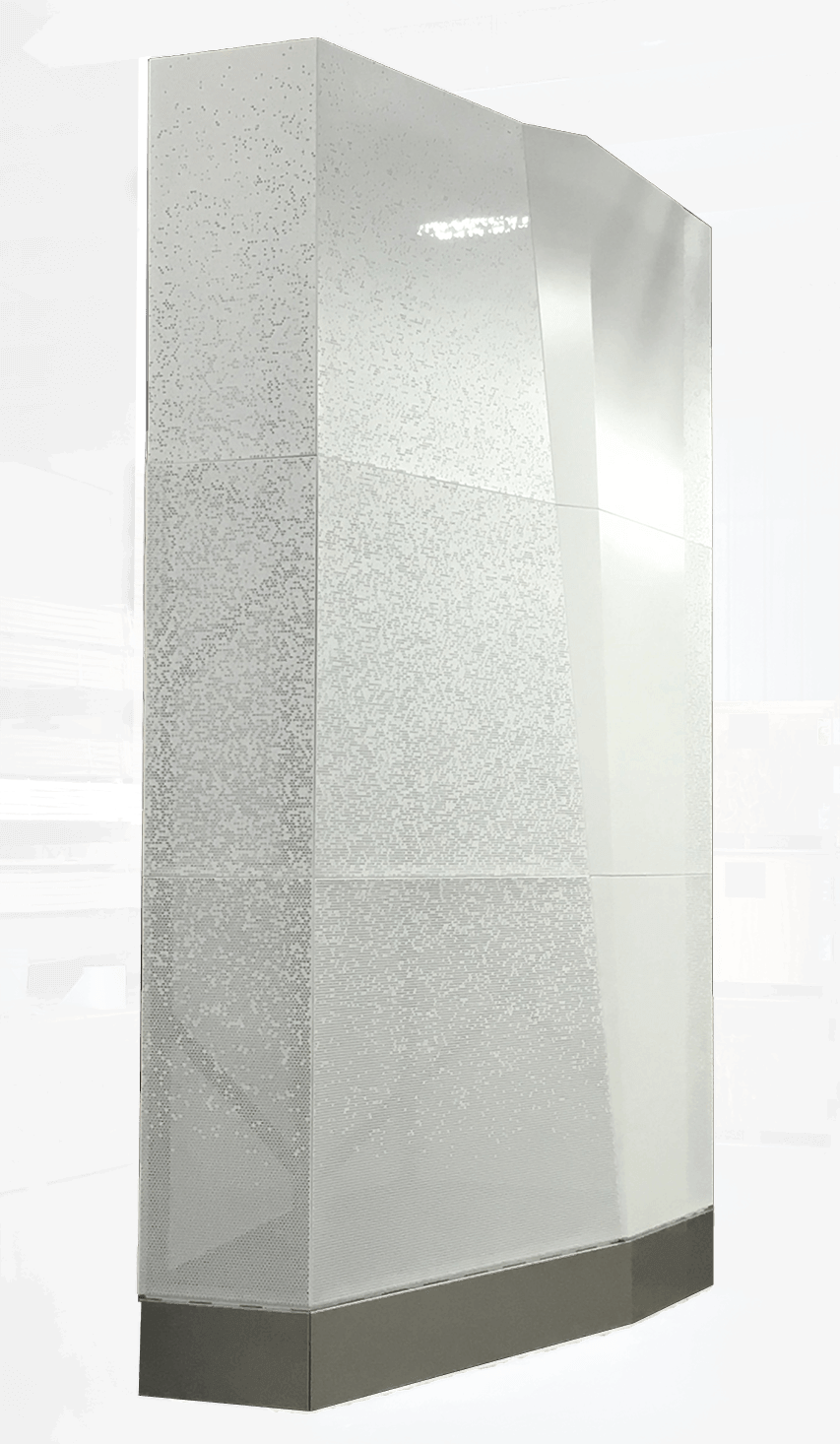
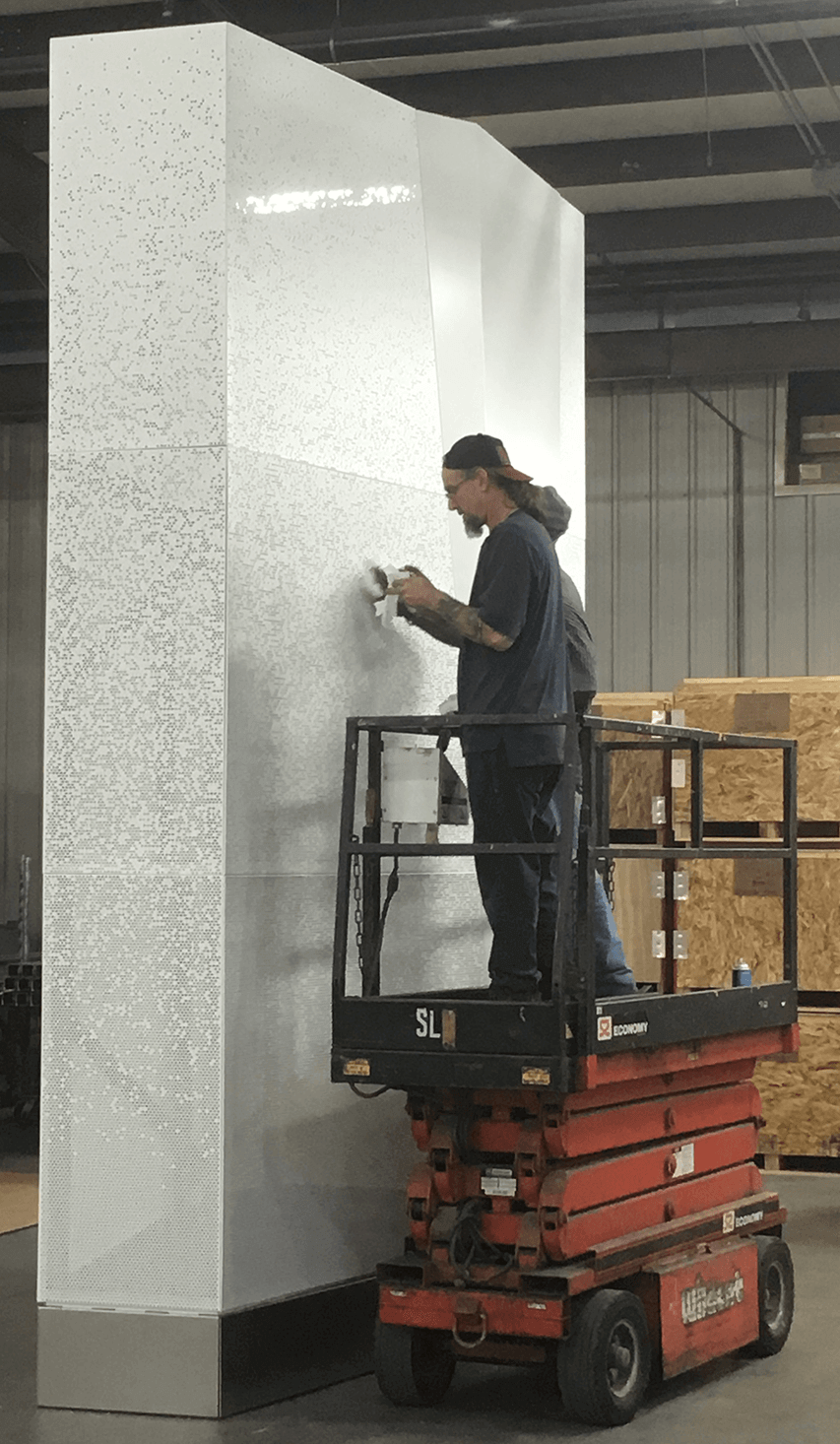

Progress
At the project site, installation of the column covers was coordinated with several M.E.P contractors. HVAC air flow testing was required post assembly of the column covers before Phase 1 of the terminal was allowed to open, on schedule.
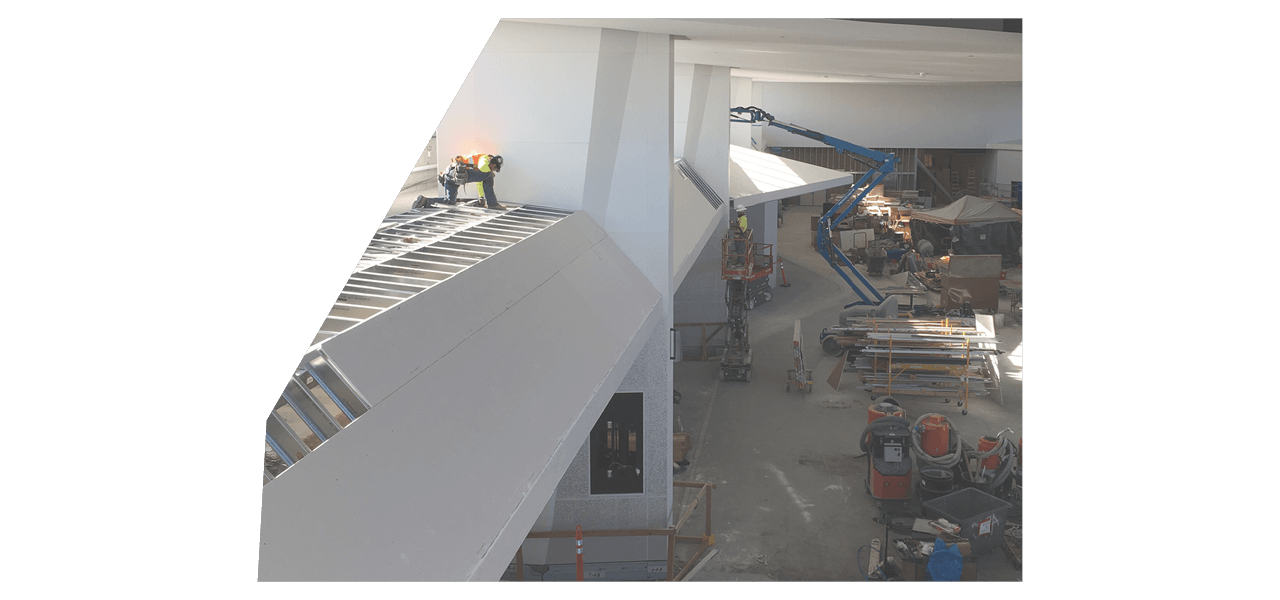
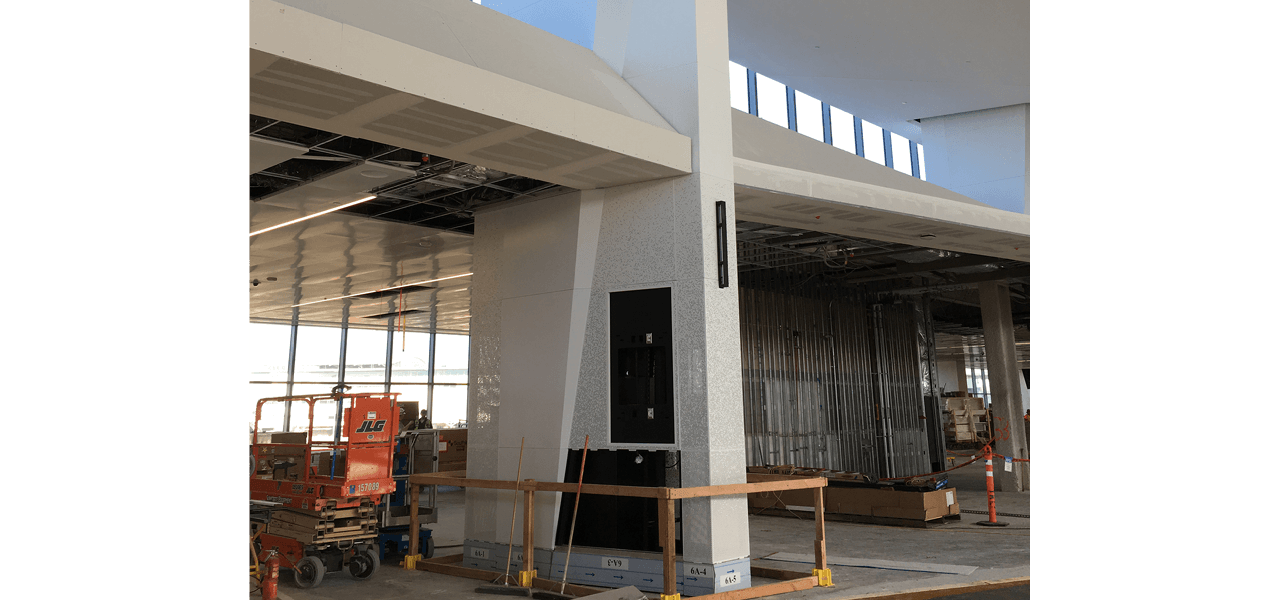
From Rendering to Reality…
Gordon Incorporated provided 119 uniquely shaped, custom column covers for Phase 1 of the $2.4 billion San Francisco International Airport Harvey Milk Terminal 1. Upper column skin materials were customized to meet architectural design objectives. The perforations feature a gradient pattern that transitioned from a higher percentage of open area on the lower skins and a gradual transition in the form of a reduction in open area progressing to the top of the column.
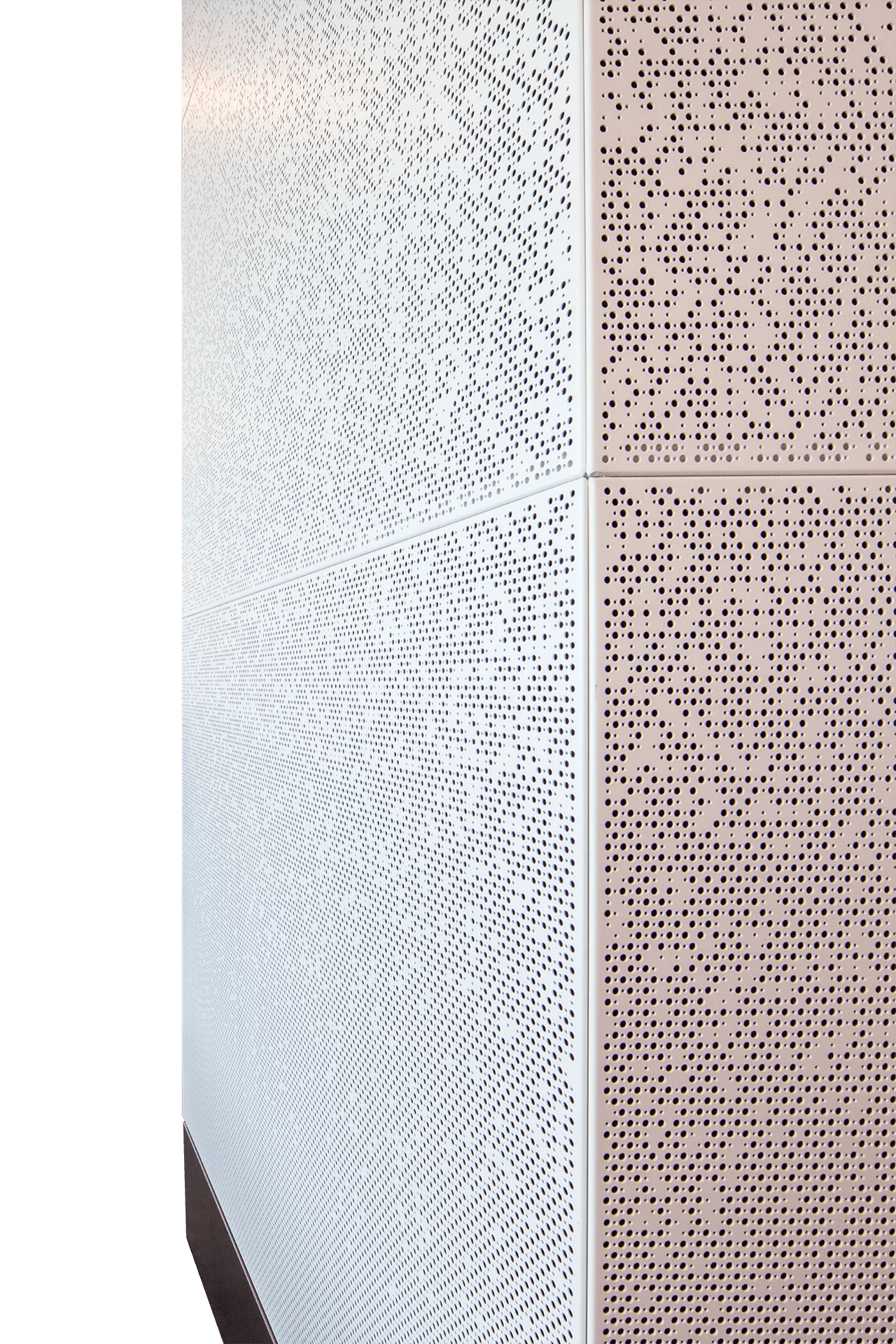
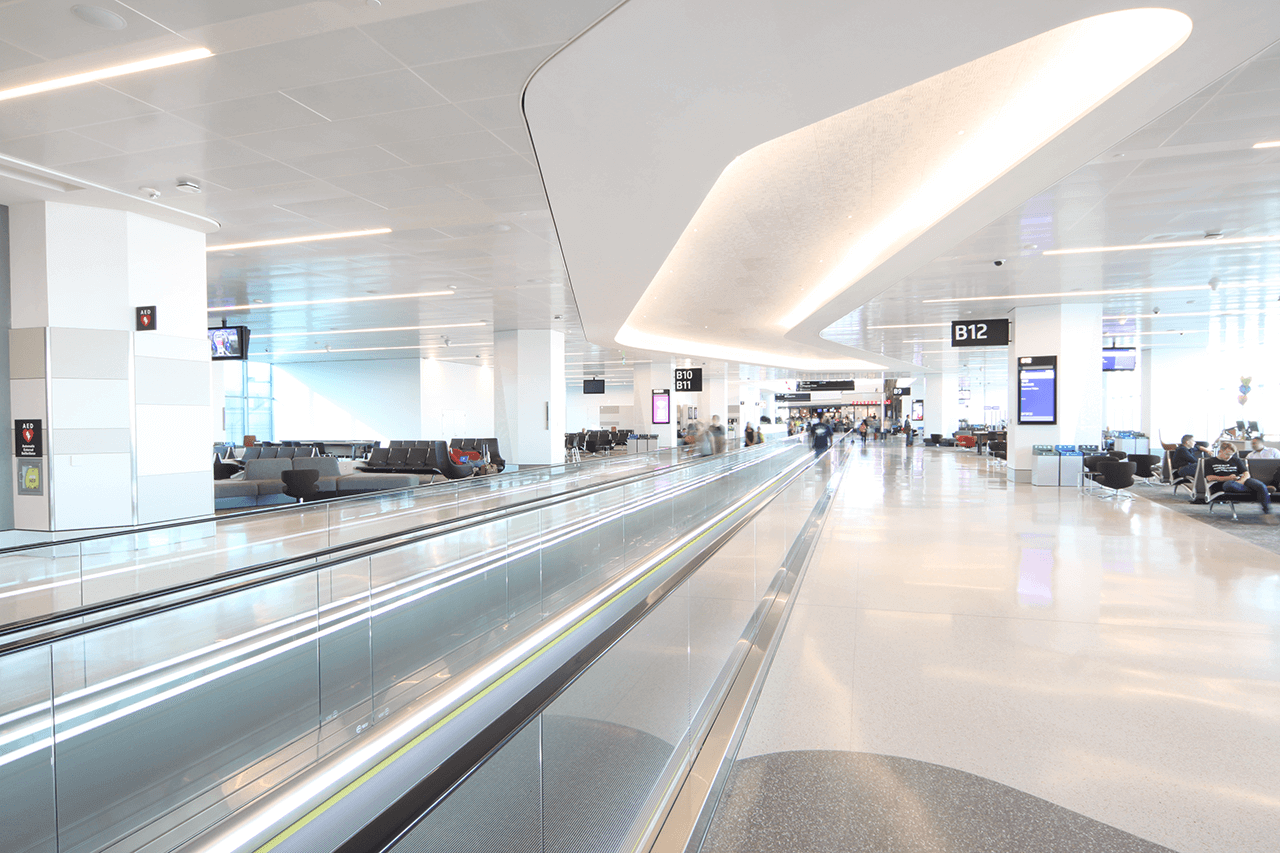
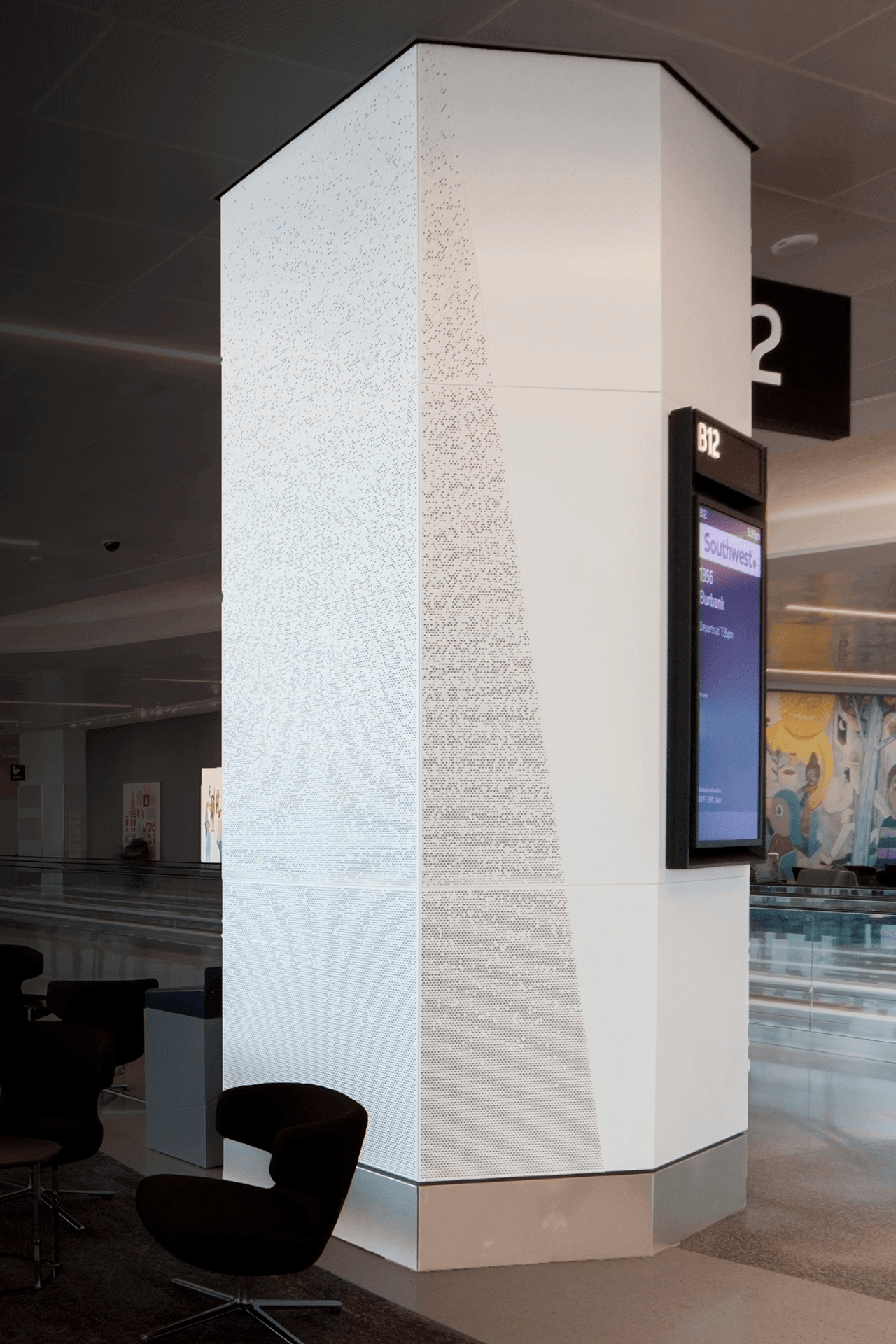
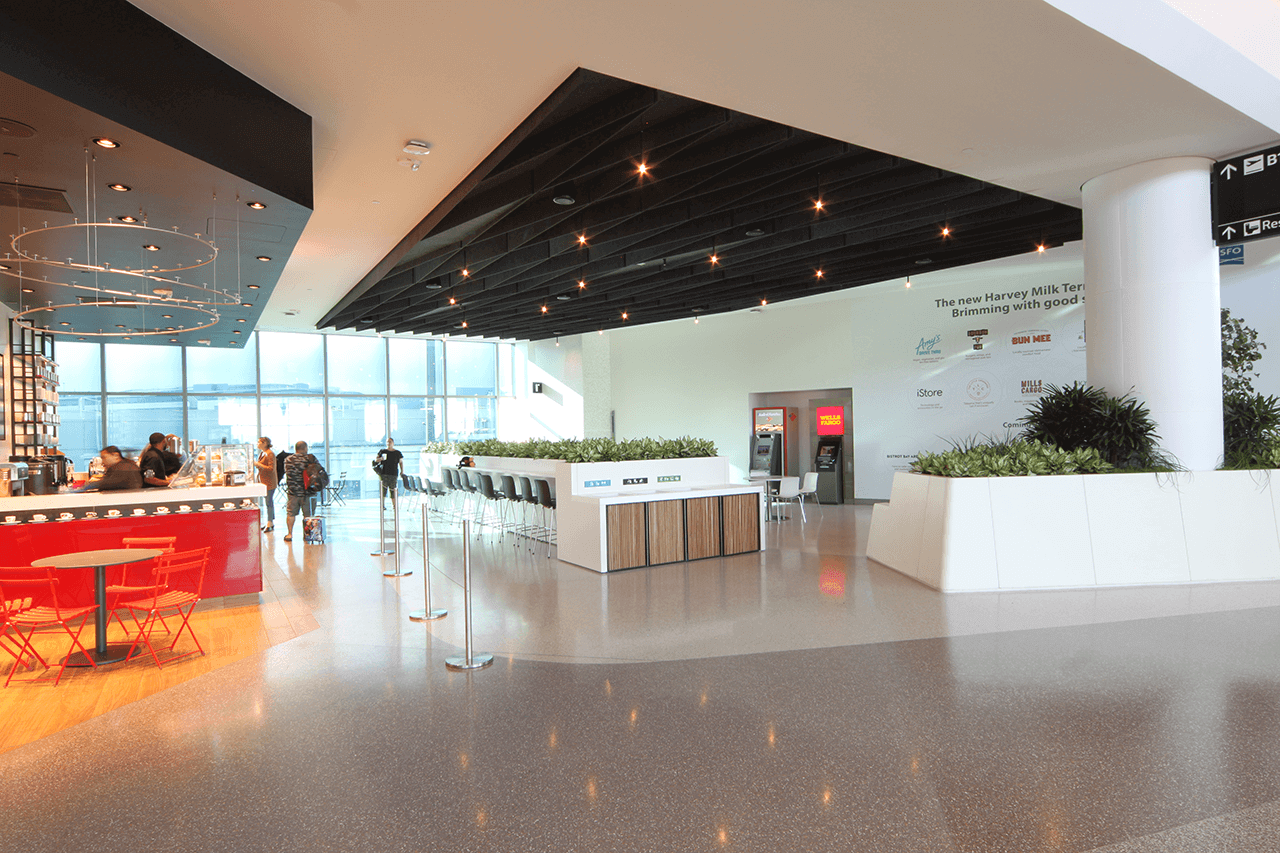